June 2015
Another Problem
13/06/15 09:35
We all assumed the joists were the same depth in both the main house and the rear outrigger. We were wrong, the outrigger joists are only around 150mm (6 inches) deep compared to the 175ish (7 inches) depth in the main house. In addition the existing floor is not level. The joists also need realigning since they are not level (almost flush with the bottom of the new steel on the north wall but much below it at the south wall).
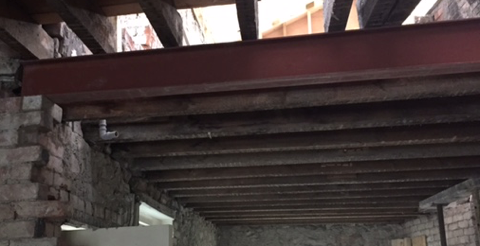
The photo below shows the slope to the south more clearly.
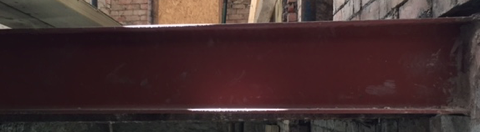
What to do? We need the room in the Kitchen below to carry the MVHR ducting without interfering with opening the back door so the joists need to be flush with the base of the steel. The 203mm steel wouldn't work with 150mm joists and approx 20mm subfloor - another 30 mm would be required to get the level to the top of the steel.
The various solutions all seem to involve the same amounts of labour but we have decided to buy new deeper joists. The main benefits are that the maximum length of over 3.5m is much too far for a 150mm joist anyway and we can now hang the new joists directly from the wall rather than carry on with joist pockets.
Pocketed joists are not a good idea - the photo below is from the ground floor
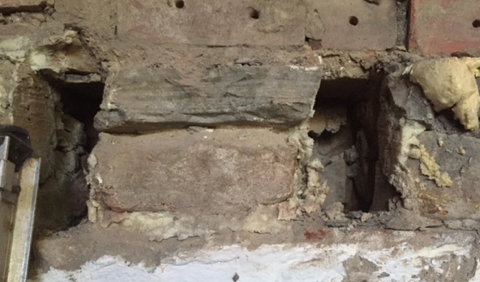
The joists that came out from these are generally in a very poor state from moisture damage over the last 100+years - see below.
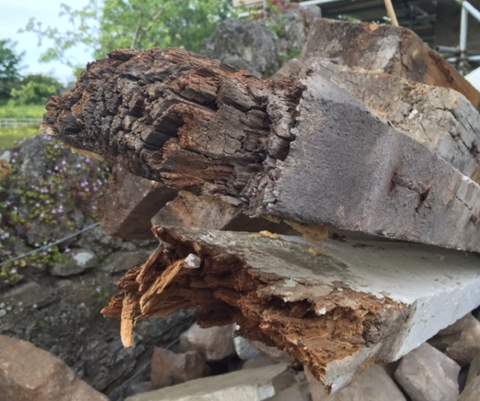
A big advantage of filling in the pockets with masonry is that it will provide additional strength to the existing wall and will also be very easy to parge and get airtight.
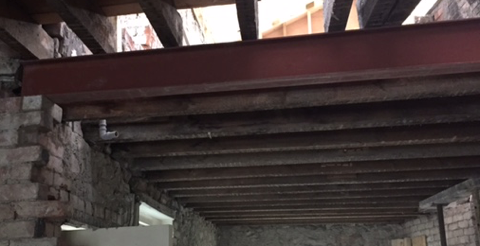
The photo below shows the slope to the south more clearly.
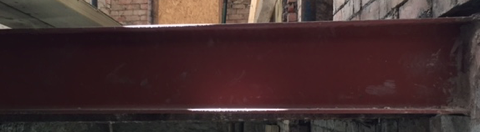
What to do? We need the room in the Kitchen below to carry the MVHR ducting without interfering with opening the back door so the joists need to be flush with the base of the steel. The 203mm steel wouldn't work with 150mm joists and approx 20mm subfloor - another 30 mm would be required to get the level to the top of the steel.
The various solutions all seem to involve the same amounts of labour but we have decided to buy new deeper joists. The main benefits are that the maximum length of over 3.5m is much too far for a 150mm joist anyway and we can now hang the new joists directly from the wall rather than carry on with joist pockets.
Pocketed joists are not a good idea - the photo below is from the ground floor
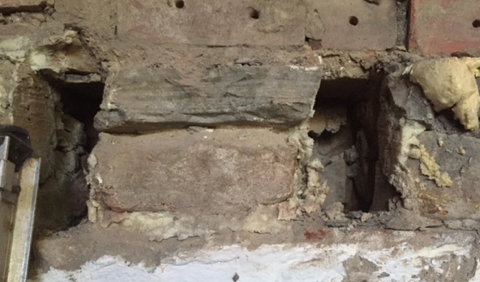
The joists that came out from these are generally in a very poor state from moisture damage over the last 100+years - see below.
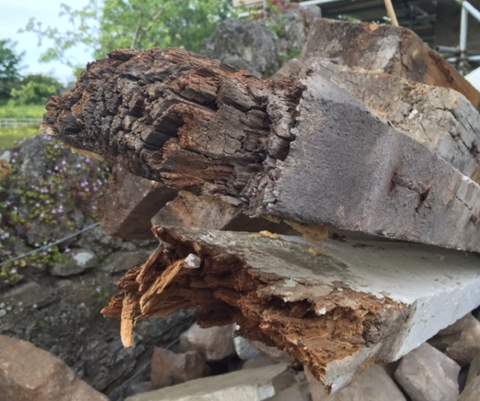
A big advantage of filling in the pockets with masonry is that it will provide additional strength to the existing wall and will also be very easy to parge and get airtight.
Demolition continues
02/06/15 17:52
The builders started work around 10 weeks ago and demolition continues to dominate. Just the basement remains and the photo below is of the rear with the old back door (with cat flap) to the top right. Henry, as usual is removing the debris to the skip.
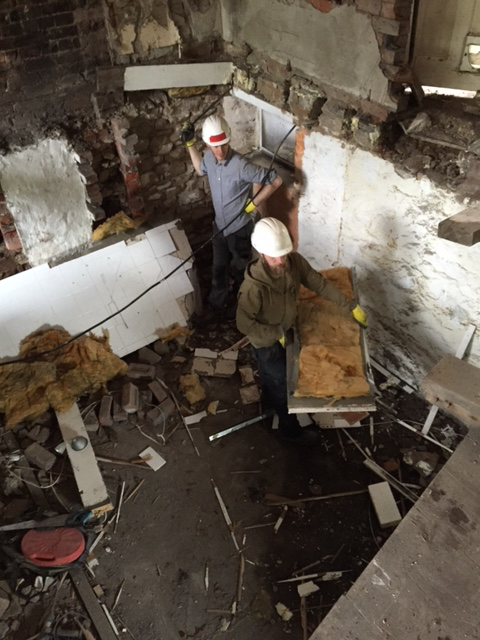
It is not all demolition - the penultimate steel has now been positioned and work on the roof continues. Progress here now really awaits the Burlington slate delivery. The old light wells and the voids that the Chimney Breast removal revealed on the Party Wall are now bricked up
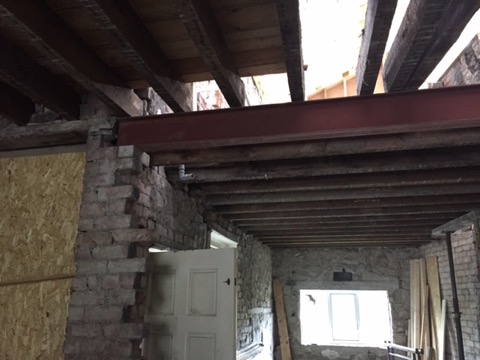
We still need to finalise all the room layouts so the builders can provide necessary plumbing and electrics. At least we have the bath sorted. This will be from the Cabuchon factory in Morecambe - always good to support local suppliers - and yes it does have a seat.
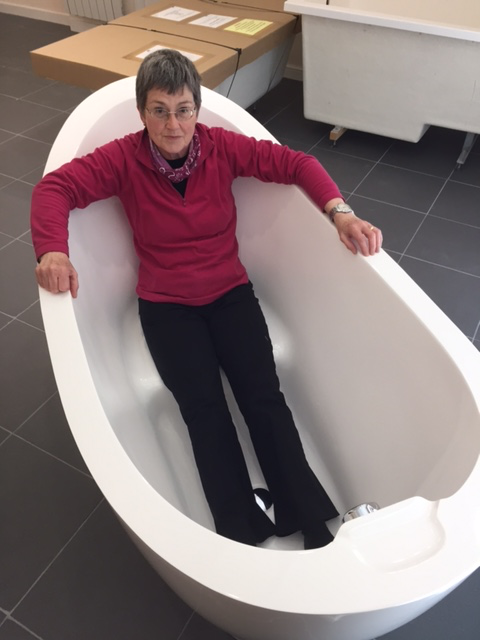
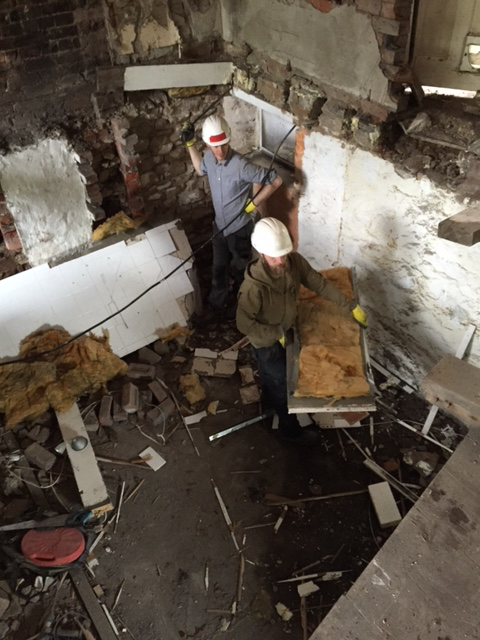
It is not all demolition - the penultimate steel has now been positioned and work on the roof continues. Progress here now really awaits the Burlington slate delivery. The old light wells and the voids that the Chimney Breast removal revealed on the Party Wall are now bricked up
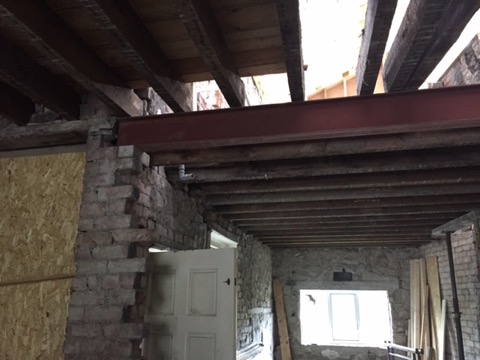
We still need to finalise all the room layouts so the builders can provide necessary plumbing and electrics. At least we have the bath sorted. This will be from the Cabuchon factory in Morecambe - always good to support local suppliers - and yes it does have a seat.
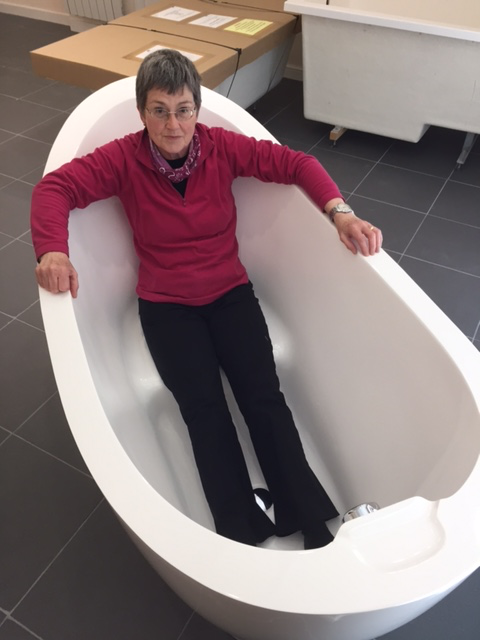