May 2016
Slow but Sure
30/05/16 17:37
The Glass Splash Backs have been fitted in the Kitchen and the glass around the stairs fitted - they both look very good.
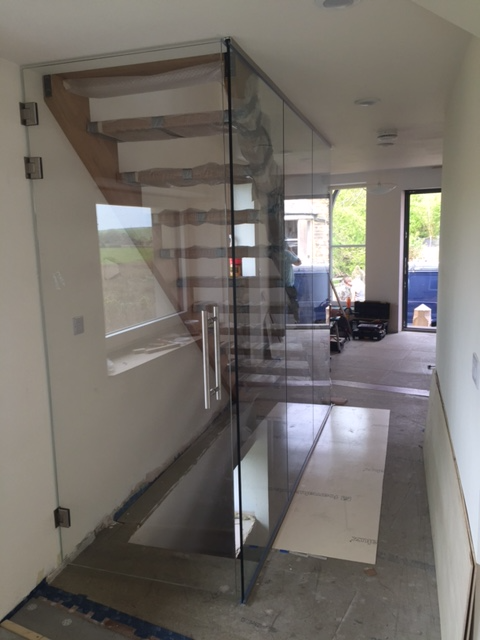
We also hoped to have the glass stair risers fitted by now but the first batch arrived looking much too white. Replacements are now here so these should be fitted in the next couple of weeks. We had also expected to finish the floor tiling in the Kitchen but that has also been delayed because the tile cutter motor burnt out!
Attention moved to the Utility area of the Basement and this presented the challenge of a very uneven floor. Eventually we sorted out the key reference level for the base cupboard support rail and most of the units are now installed. (Below is the situation about a week ago).
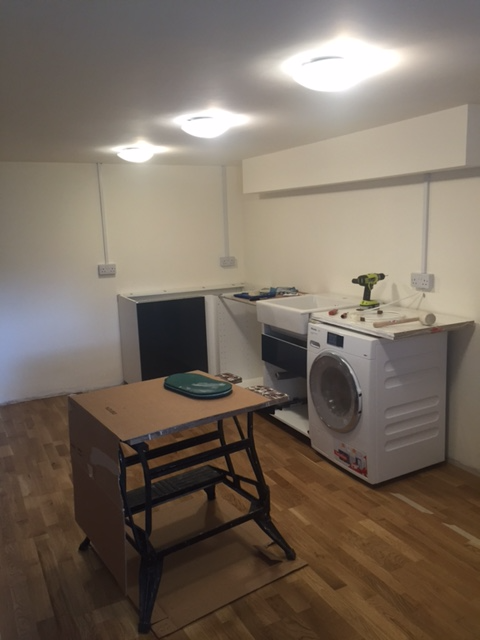
The washing machine now sits on a plywood base and is level to within 0.5mm - not bad for a couple of pensioners struggling with a 100kg machine. The plumbing is also now complete and leak free. However it is still not finished. We started with testing the waste run to the pumped Sanivite unit and the vertical connection back into the main soil pipe. We had leaks from two of the jubilee clips which needed tightening. Having done this we still had a leak from somewhere - not good on a wood floor. We turned everything off and took the Sanivite until upstairs to investigate further. It had a very small crack in the base moulding that was the source of the leak. (Near the top of the recess in the photo below).
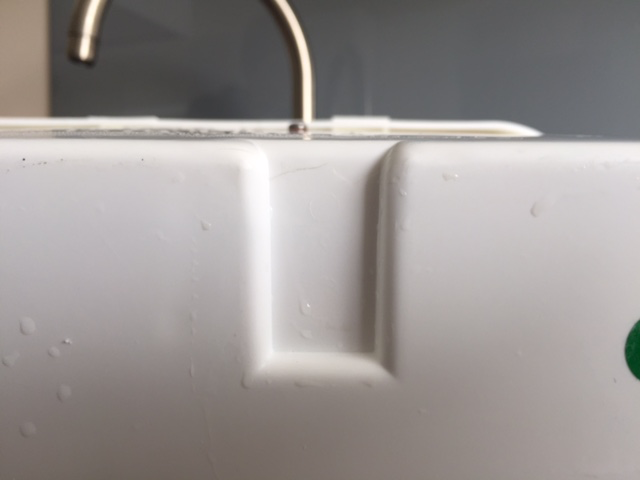
The local Saniflo engineer was on the premises within a few hours and a replacement casing has been ordered.
We finally decided to order the main flooring material last week - we went for 20mm engineered oak flooring. We need to leave it in the house for a few weeks before laying in order for the wood to adjust to the humidity of the house. Hopefully the 87 sq.m. from Havwoods will be sufficient. Both Glenys and I needed a break after carrying it into the house - the half that was stored on the first floor was rather wearing.
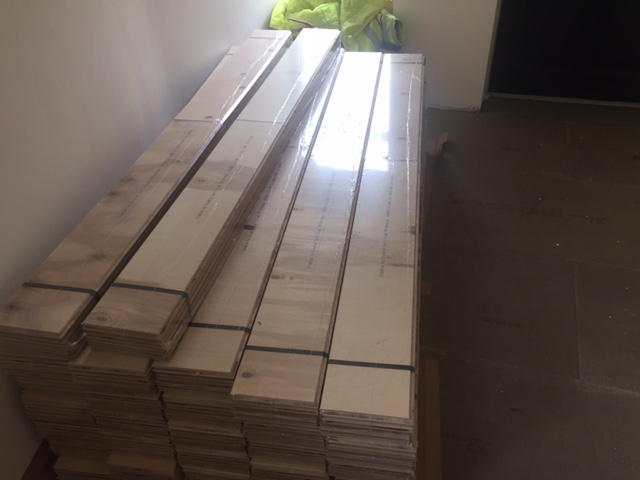
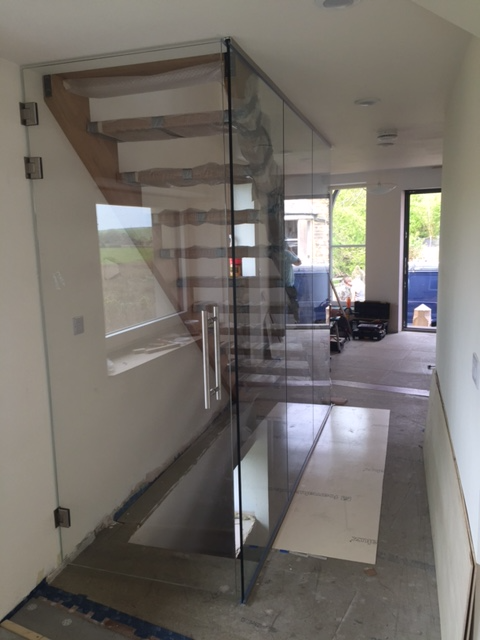
We also hoped to have the glass stair risers fitted by now but the first batch arrived looking much too white. Replacements are now here so these should be fitted in the next couple of weeks. We had also expected to finish the floor tiling in the Kitchen but that has also been delayed because the tile cutter motor burnt out!
Attention moved to the Utility area of the Basement and this presented the challenge of a very uneven floor. Eventually we sorted out the key reference level for the base cupboard support rail and most of the units are now installed. (Below is the situation about a week ago).
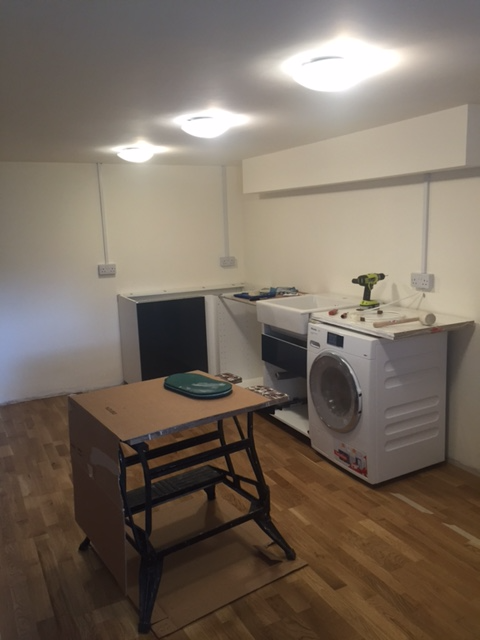
The washing machine now sits on a plywood base and is level to within 0.5mm - not bad for a couple of pensioners struggling with a 100kg machine. The plumbing is also now complete and leak free. However it is still not finished. We started with testing the waste run to the pumped Sanivite unit and the vertical connection back into the main soil pipe. We had leaks from two of the jubilee clips which needed tightening. Having done this we still had a leak from somewhere - not good on a wood floor. We turned everything off and took the Sanivite until upstairs to investigate further. It had a very small crack in the base moulding that was the source of the leak. (Near the top of the recess in the photo below).
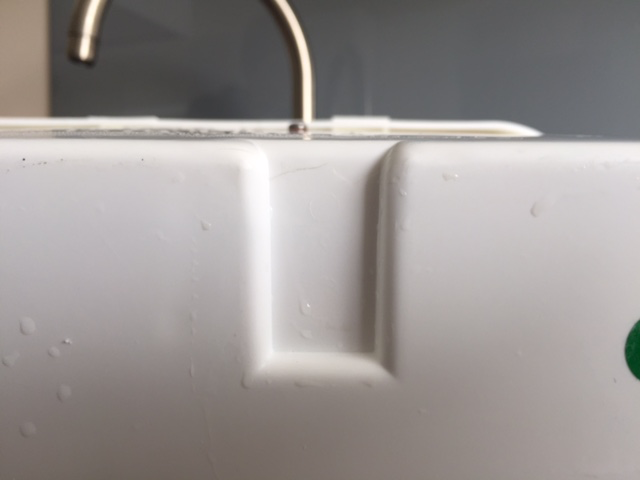
The local Saniflo engineer was on the premises within a few hours and a replacement casing has been ordered.
We finally decided to order the main flooring material last week - we went for 20mm engineered oak flooring. We need to leave it in the house for a few weeks before laying in order for the wood to adjust to the humidity of the house. Hopefully the 87 sq.m. from Havwoods will be sufficient. Both Glenys and I needed a break after carrying it into the house - the half that was stored on the first floor was rather wearing.
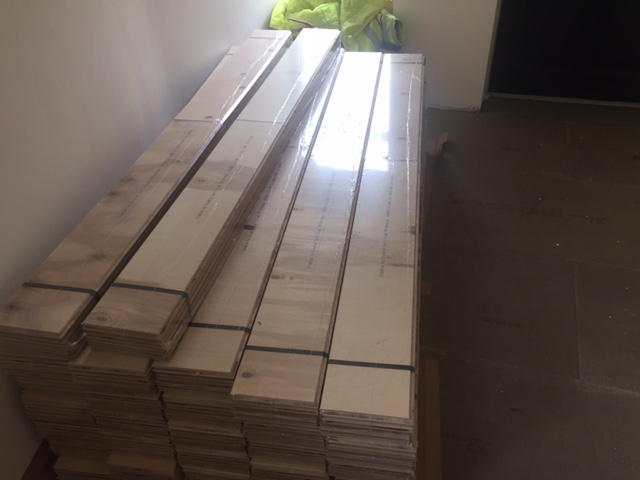
Steady Progress
01/05/16 17:36
Today we tried out the shower for the first time, it performed well and we didn't miss the deleted shower screen - the water drops were mostly confined to 1 metre from the shower head. We have also used the bath on two occasions and the Sunamps provide sufficient water for the full immersive bath experience - up to the overflow. However one of the SunampPV units needs a new thermal over temperature switch - apparently the ones supplied to Sunamp were not up to specification and I am promised replacements for the two units. At least we can now keep them charged from the surplus electricity from the PV system. The changes to our supply (and others in the road) made a month ago by Electricity North West have kept the Inverter working.
April was the first month I could record the output of the PV system and it seems promising given the shading we experience from Chimney Stacks and Chimney Pots.
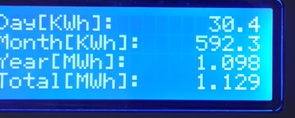
Work continues in the Kitchen with Glenys and I laying floor tiles - the Kitchen is still good to look at and work in and we expect Butlers back soon to fit the two glass splashbacks.
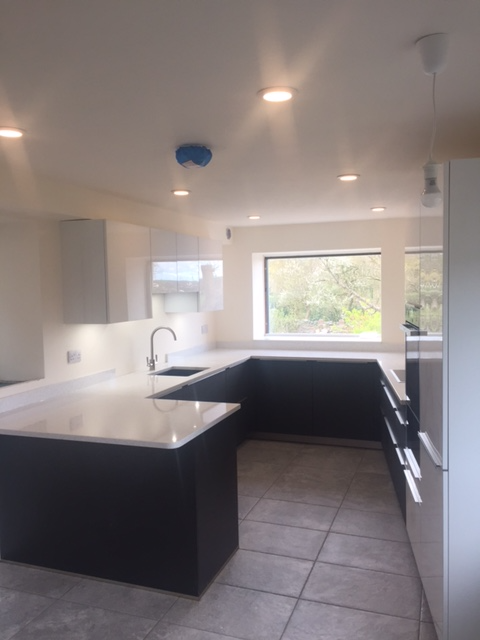
Later next week Stairs and more are back to install the glass around the stairs. (We both look forward to seeing the finished product.) Before then we need to check the painting around the stairwells. Glenys tells me we started painting on the 10th February and we still have several days painting left to do. This wasn't how it was expected to go. The plan was to start on the first floor and work down in a systematic and logical manner. Trouble is we were forced to jump around the house because of other workmen. Paint the ceilings about pendent lights, paint the walls around switches, sockets and wall lights. Paint the Kitchen so the units can be installed. Paint the stairwells ahead of the stairs etc etc.
April was the first month I could record the output of the PV system and it seems promising given the shading we experience from Chimney Stacks and Chimney Pots.
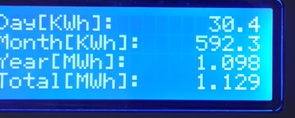
Work continues in the Kitchen with Glenys and I laying floor tiles - the Kitchen is still good to look at and work in and we expect Butlers back soon to fit the two glass splashbacks.
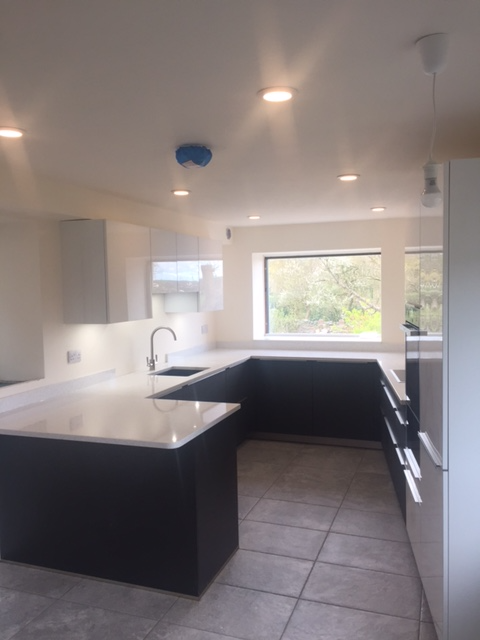
Later next week Stairs and more are back to install the glass around the stairs. (We both look forward to seeing the finished product.) Before then we need to check the painting around the stairwells. Glenys tells me we started painting on the 10th February and we still have several days painting left to do. This wasn't how it was expected to go. The plan was to start on the first floor and work down in a systematic and logical manner. Trouble is we were forced to jump around the house because of other workmen. Paint the ceilings about pendent lights, paint the walls around switches, sockets and wall lights. Paint the Kitchen so the units can be installed. Paint the stairwells ahead of the stairs etc etc.