November 2015
We hope for dry weather
25/11/15 17:49
The wind and rain of the last few weeks meant that the top coat covering the external render on the Gable Wall only went on this morning. Hopefully the rain will hold off now for at least 36 hours in order to allow it 'go off'.
Over the last couple of weeks the Pegasus workmen have been remarkably stalwart in the face of driving wind and rain - managing to fix the insulation and even applying the base render in the brief weather windows.
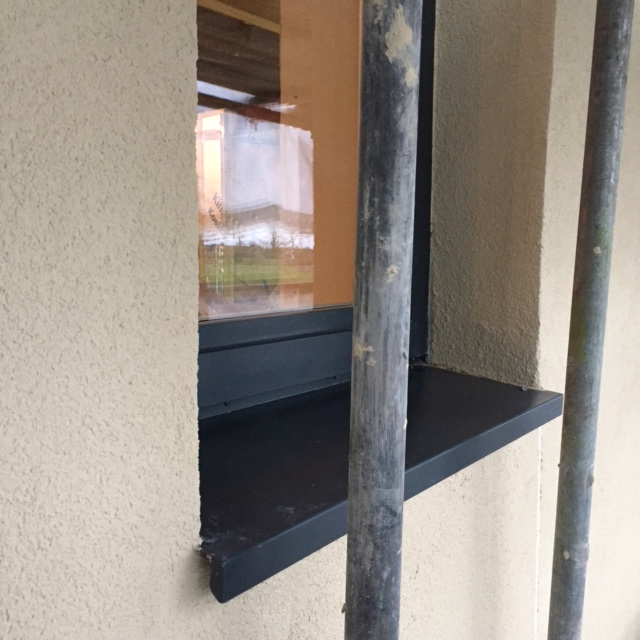
Dean, the Stonemason, has been busy repointing the front elevation and re-laying the front garden wall
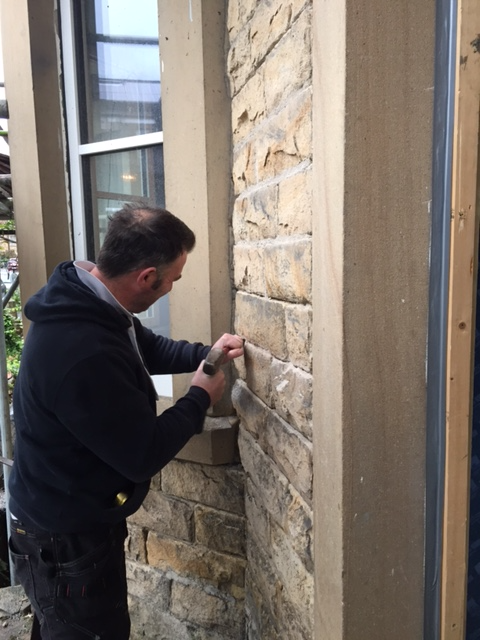
Internal progress is steady. In the basement the vips are now down and the final flooring laid. This was accomplished very quickly because the fragile vacuum panels couldn't remain unprotected for long. Even so we lost a second panel for no particular reason.
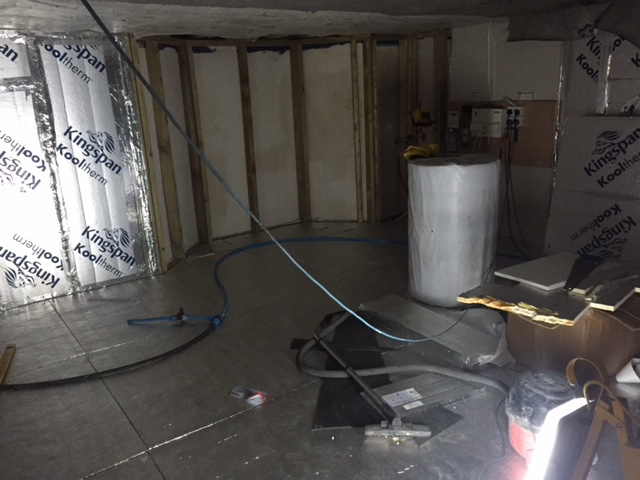
Eden Insulation managed to blow the 750mm Warmcell insulation into the loft in less than two days. This job was not very pleasant for the installers who turned into grey fluff balls. The cellulose fluff also managed to deposit itself all over the first floor which required some diligent work by the 'cleaning fairies'. It is working well according to Gideon who looked at the roof as he commuted to work on the train on the first frosty morning of the season. He noted the pristine white roof in comparison to the rest of the street.
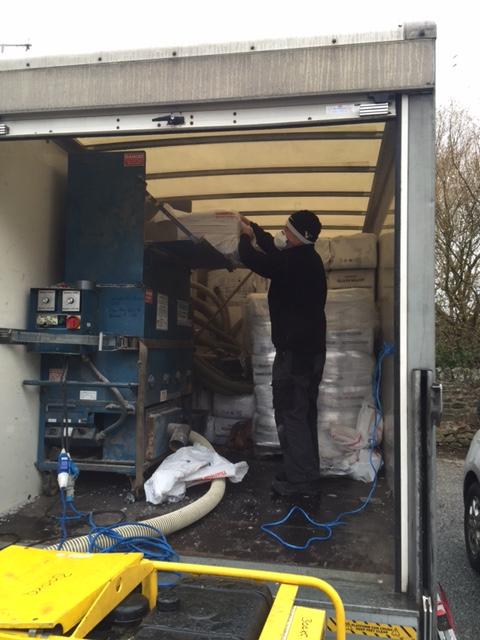
And stud walls are going in, as is the first fix wiring. Photo shows part of Bedroom 2 with the Bathroom behind. The corridor on the right tapers as it goes through to Paul's Study at the back.
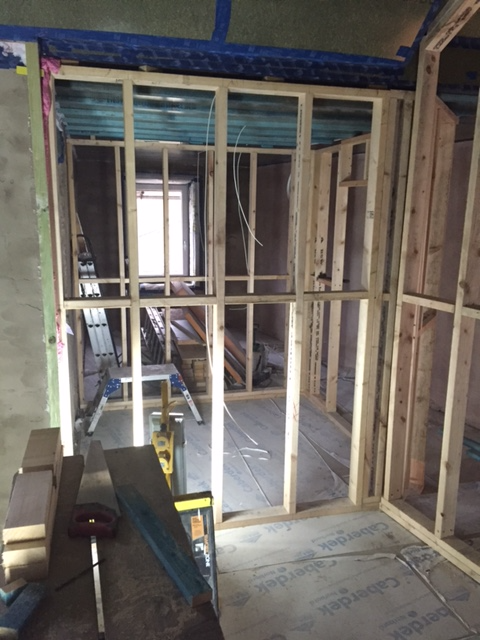
Over the last couple of weeks the Pegasus workmen have been remarkably stalwart in the face of driving wind and rain - managing to fix the insulation and even applying the base render in the brief weather windows.
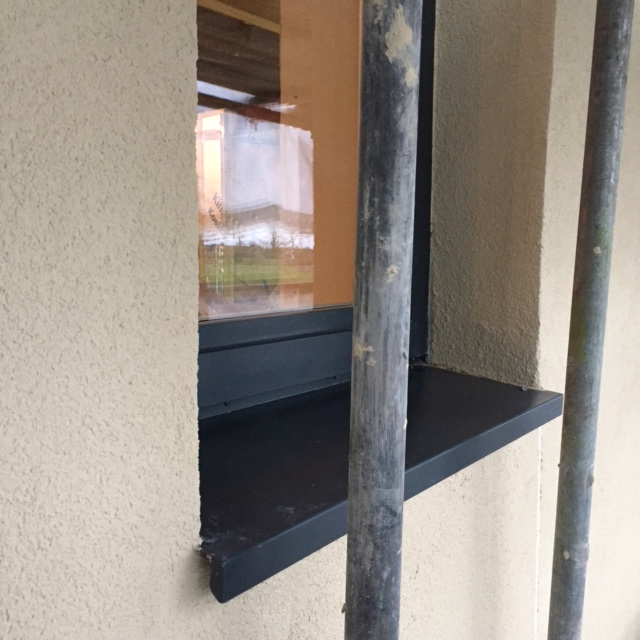
Dean, the Stonemason, has been busy repointing the front elevation and re-laying the front garden wall
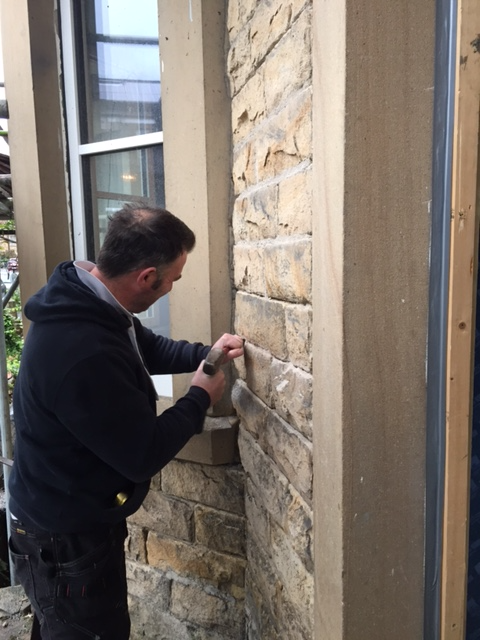
Internal progress is steady. In the basement the vips are now down and the final flooring laid. This was accomplished very quickly because the fragile vacuum panels couldn't remain unprotected for long. Even so we lost a second panel for no particular reason.
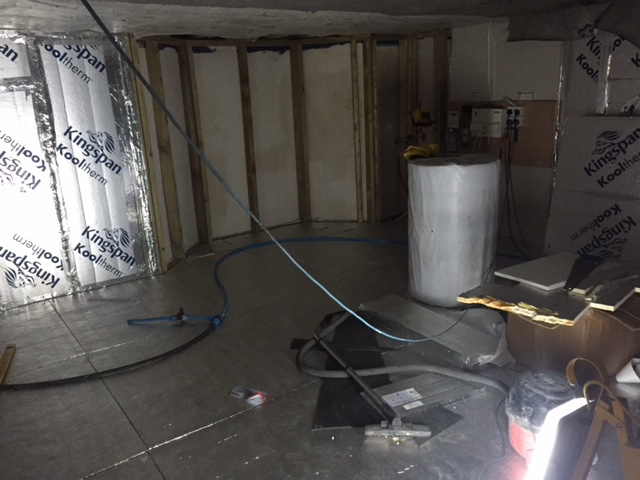
Eden Insulation managed to blow the 750mm Warmcell insulation into the loft in less than two days. This job was not very pleasant for the installers who turned into grey fluff balls. The cellulose fluff also managed to deposit itself all over the first floor which required some diligent work by the 'cleaning fairies'. It is working well according to Gideon who looked at the roof as he commuted to work on the train on the first frosty morning of the season. He noted the pristine white roof in comparison to the rest of the street.
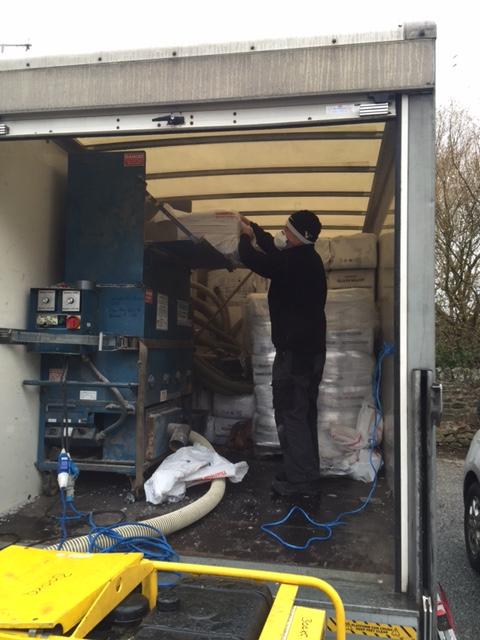
And stud walls are going in, as is the first fix wiring. Photo shows part of Bedroom 2 with the Bathroom behind. The corridor on the right tapers as it goes through to Paul's Study at the back.
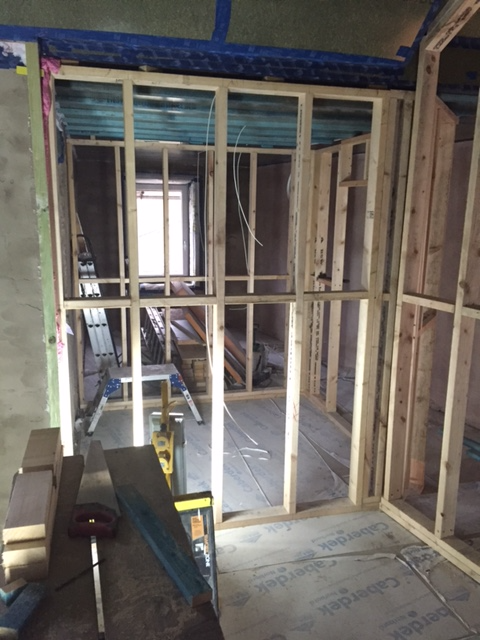
Winter approaches
08/11/15 15:55
The last week has been wet and windy and this weather is likely to continue into next week. Just in time for Pegasus to arrive and commence the external insulation. With the benefit of sheathing they managed to almost finish fixing the insulation to the gable wall. They still have to manage the window detailing before the render can be applied. Since the render needs dry weather I am not expecting this to be achieved next week. The window sills can at least be fixed though.
On the front elevation Dean (the Stonemason) has refurbished damaged stone cills and is now preparing to repoint. At least half of this area is sheltered from the rain and the hydraulic lime loves the high humidity so something should be achieved next week.
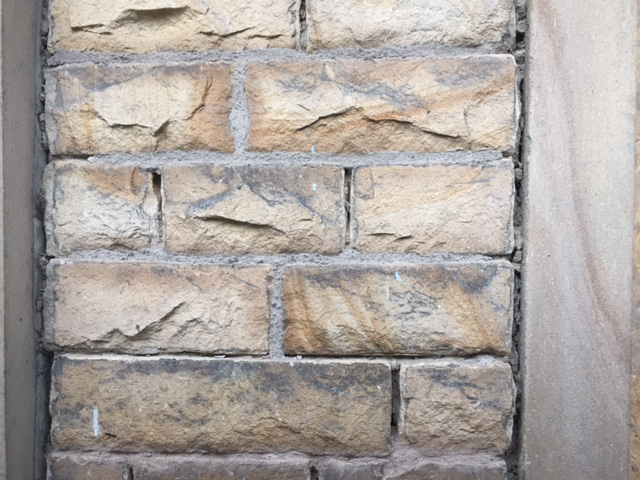
The experts amongst you will be able to discern the differences between the different mortar mix samples in the photo above - there are four mixes. The bottom one is builders sand and lime with no aggregate. The three at the top have white sand and aggregate in addition. We have chosen the second from the top as the best match to the original. As the client it is amazing the variety of decisions you are required to make - usually with severe time pressure.
We were planning to use linoleum on the floor of the Basement as well as the Bathroom but this might not happen. The flooring person came around last week to measure up and thinks the adhesive will only work with plywood as it reacts with many other wood based products. We briefly thought 8mm ply could be used instead of laminate but worry movement along the joints will destroy both the linoleum and the vacuum Insulation panels below (3mm of foam not withstanding). We are now thinking of just finishing with a 10mm engineered wood floor with a locking joint. This would simplify the floor build up and probably save money.
On the front elevation Dean (the Stonemason) has refurbished damaged stone cills and is now preparing to repoint. At least half of this area is sheltered from the rain and the hydraulic lime loves the high humidity so something should be achieved next week.
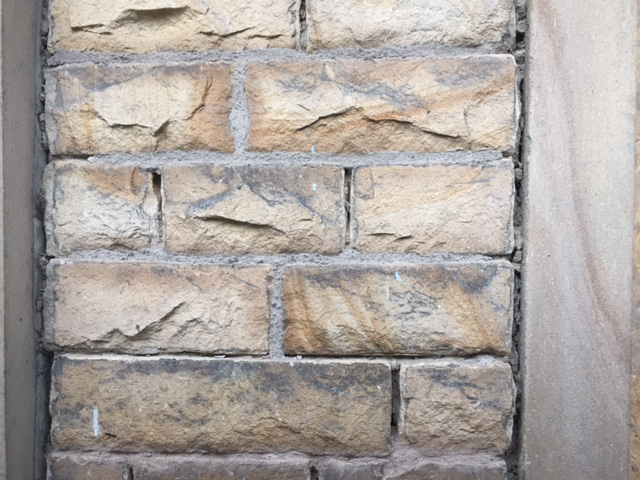
The experts amongst you will be able to discern the differences between the different mortar mix samples in the photo above - there are four mixes. The bottom one is builders sand and lime with no aggregate. The three at the top have white sand and aggregate in addition. We have chosen the second from the top as the best match to the original. As the client it is amazing the variety of decisions you are required to make - usually with severe time pressure.
We were planning to use linoleum on the floor of the Basement as well as the Bathroom but this might not happen. The flooring person came around last week to measure up and thinks the adhesive will only work with plywood as it reacts with many other wood based products. We briefly thought 8mm ply could be used instead of laminate but worry movement along the joints will destroy both the linoleum and the vacuum Insulation panels below (3mm of foam not withstanding). We are now thinking of just finishing with a 10mm engineered wood floor with a locking joint. This would simplify the floor build up and probably save money.